As we saw in Part-1 of our three part series on Industry 4.0, it offers several key benefits, including increased productivity, improved efficiency, enhanced automation, optimized supply chains, better decision-making through data analytics, cost savings through predictive maintenance, customization and personalization of products, and improved safety and sustainability in manufacturing processes. Like any other technology, the adoption of Industry 4.0 poses some challenges.
We all know that Small and Medium-sized Enterprises (SMEs) are the driving force of many manufacturing economies. As the backbone of the manufacturing industry, SMEs’ impact on the Fourth Industrial Revolution is significant. But they often face different challenges and barriers than larger companies.
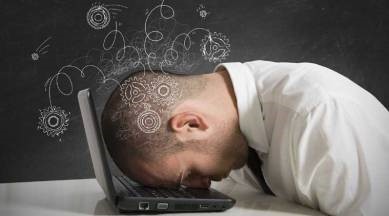
Following are some of the key challenges faced by SMEs for adopting Industry 4.0 in their products:
1) Limited Resources: Small manufacturers often have limited financial and human resources to invest in digitalization initiatives. Acquiring the necessary technology, expertise, and infrastructure can be a significant hurdle.
2) Lack of Technical Expertise: Implementing digital technologies requires specialized knowledge and skills. Small manufacturers may struggle to find or afford experts who can guide them through the digital transformation process.
3) Legacy Systems and Infrastructure: Many small manufacturers still rely on outdated or legacy systems and equipment. Integrating new technologies with existing infrastructure can be complex and costly.
4) Data Management and Security: Digitalization generates vast amounts of data, and small manufacturers may face challenges in effectively managing and analyzing this data. Ensuring data security and protecting sensitive information can be particularly daunting for companies with limited cybersecurity resources.
5) Change Management: Transitioning to a digitalized environment involves cultural and organizational changes. Resistance to change, employee training, and managing the transition process can pose challenges for small manufacturers.
6) Scalability and Adaptability: Small manufacturers often face the challenge of scaling up their digital capabilities to meet growing demands or adapt to changing market trends. Ensuring that digital systems and processes can be easily scaled and adapted is crucial for long-term success.
7) Return on Investment (ROI): Small manufacturers need to carefully evaluate the potential return on investment for digitalization initiatives. Balancing the upfront costs with the expected benefits and calculating the ROI can be challenging, especially when the results may not be immediate.
8) Connectivity and Infrastructure: Connectivity issues, such as limited internet access or unreliable networks, can hinder the implementation of digital technologies. Small manufacturers may need to address infrastructure challenges to fully leverage the benefits of digitalization.
9) Market Competition: Keeping up with larger competitors who have already embraced digitalization can be a significant challenge for small manufacturers. They must find unique value propositions, niche markets, or innovative approaches to differentiate themselves.
Overcoming these challenges requires strategic planning, prioritization, and seeking support from industry experts, government initiatives, or business networks. Collaborating with technology partners, investing in employee training, and adopting a phased approach to digital transformation can help small manufacturers navigate these obstacles and unlock the benefits of digitalization. We will discuss the strategies which can be used to overcome these challenges in Part -3 of our three part series.
This article offers a fascinating perspective on the subject. The depth of research and clarity in presentation make it a valuable read for anyone interested in this topic. It’s refreshing to see such well-articulated insights that not only inform but also provoke thoughtful discussion. I particularly appreciated the way the author connected various aspects to provide a comprehensive understanding. It’s clear that a lot of effort went into compiling this piece, and it certainly pays off. Looking forward to reading more from this author and hearing other readers’ thoughts. Keep up the excellent work!